
Hedra Collection by Joshua Smith and Model No.
The mission for this collection was to create a series of furniture pieces that brought together Model No.'s dedicated sustainability mission and Joshua Smith's drive to create unique and captivating furniture. The inspiration for this collection came from the architecture of the homes owned buy Joshua Smith's clients in Palm Springs, CA. The origami-esque forms of the collection echo the clean modern lines of the mid-century homes of Palm Springs.
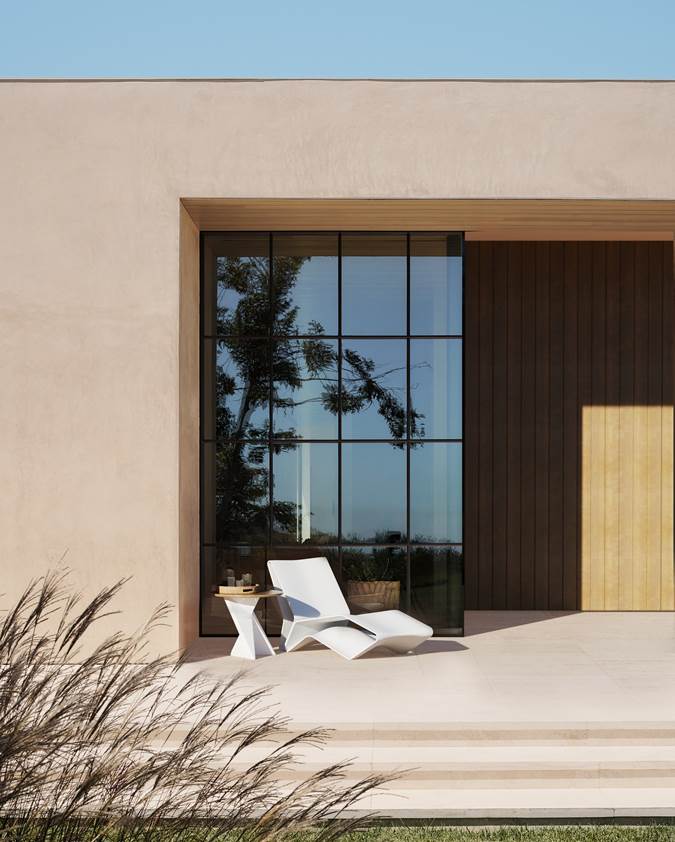
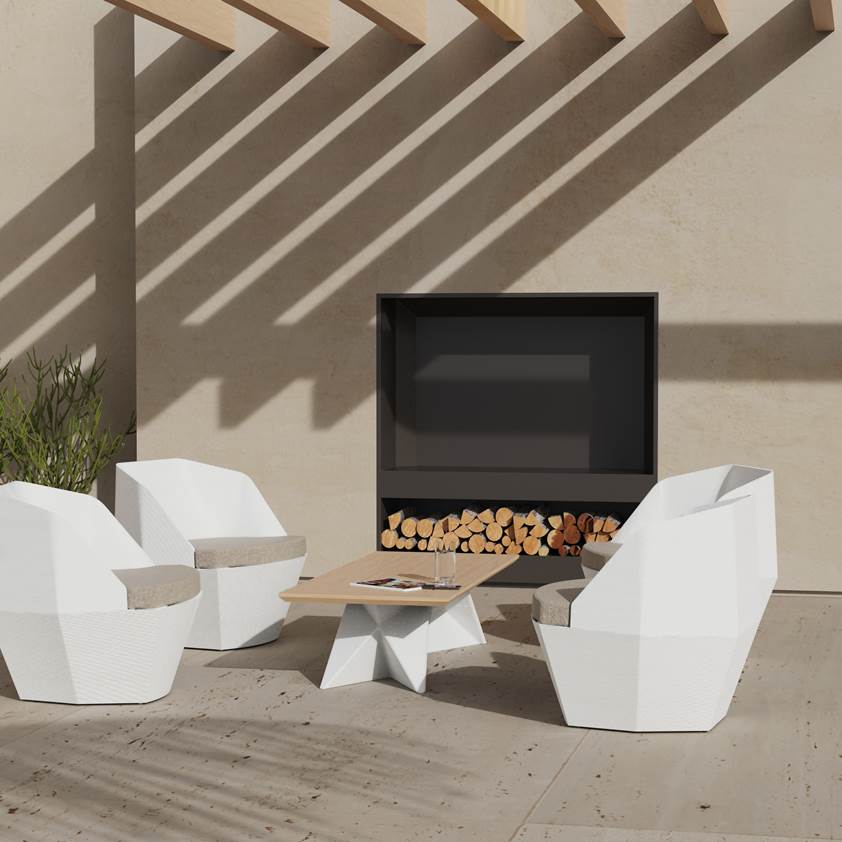
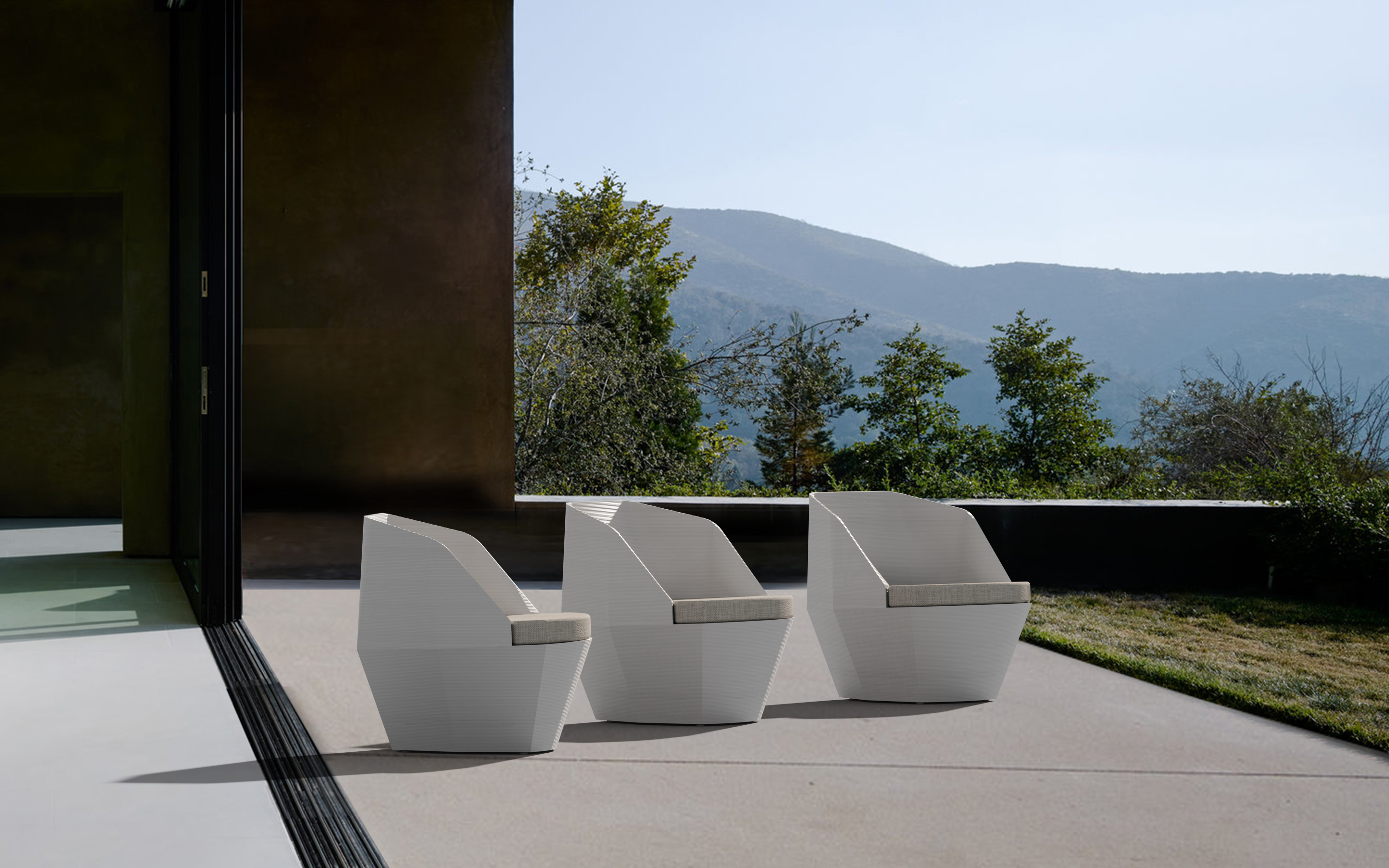
Collection Development
This collection was a collaborative effort between Joshua Smith and the design team at Model No. Our design team consists of our Director of Design, Mike Vance, Myself and Emilie Cevallos. Josuha provided us with detailed mood boards and source information to base the collection on. The design language was birthed from the first piece we developed, the side table later named "The Jasper Table."
The Jasper Table's folded paper origami aesthetic drove the form language for the rest of the collection and really pushed what we thought was possible with our manufacturing process. During prototyping phases we developed new methods to produce steeper overhang angles for our printer as well as new processes to marry two prints together in a seamless and thoughtful way.
This collection pushed the boundaries of our manufacturing process across the board driving innovation in our other product lines such as lighting and corporate furniture.
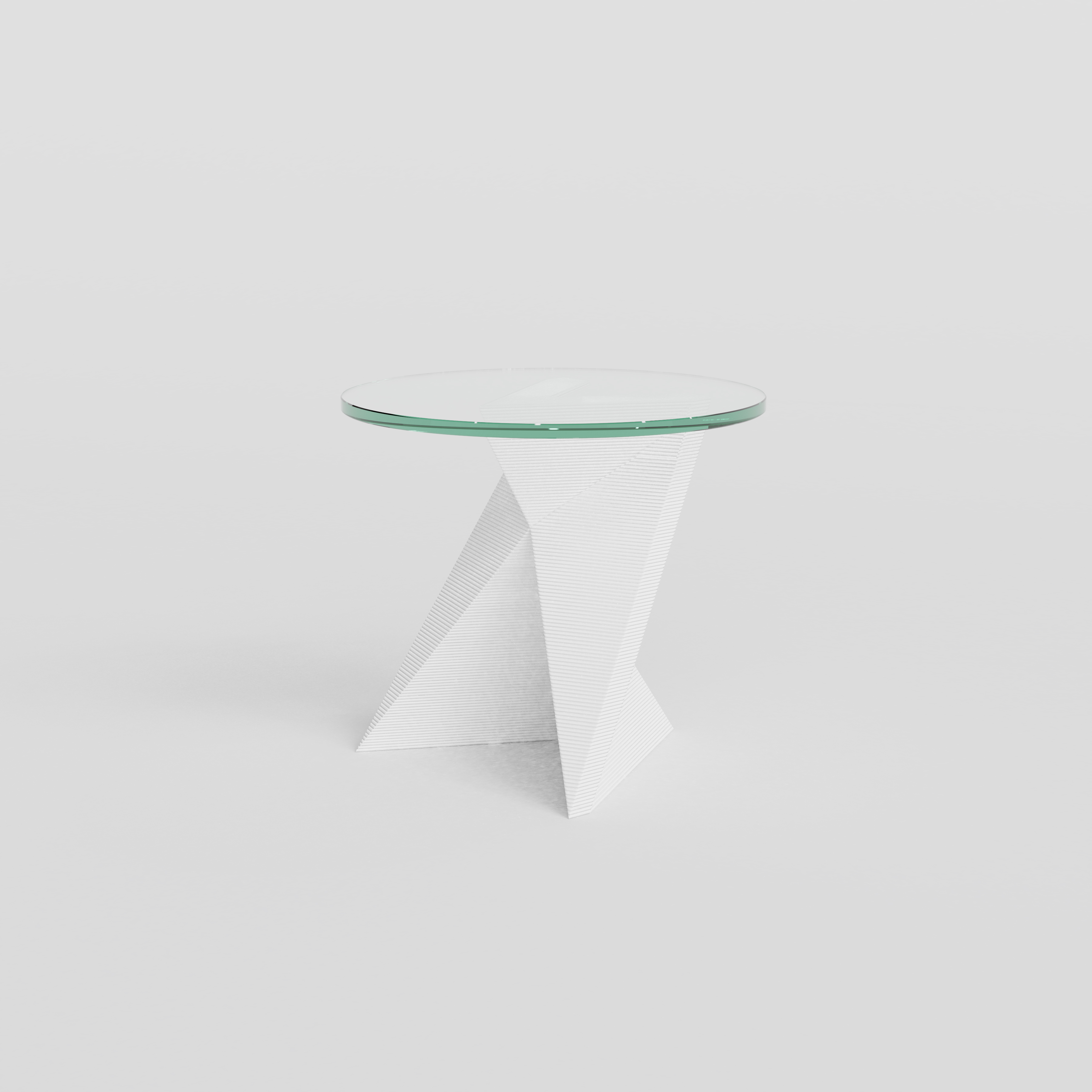
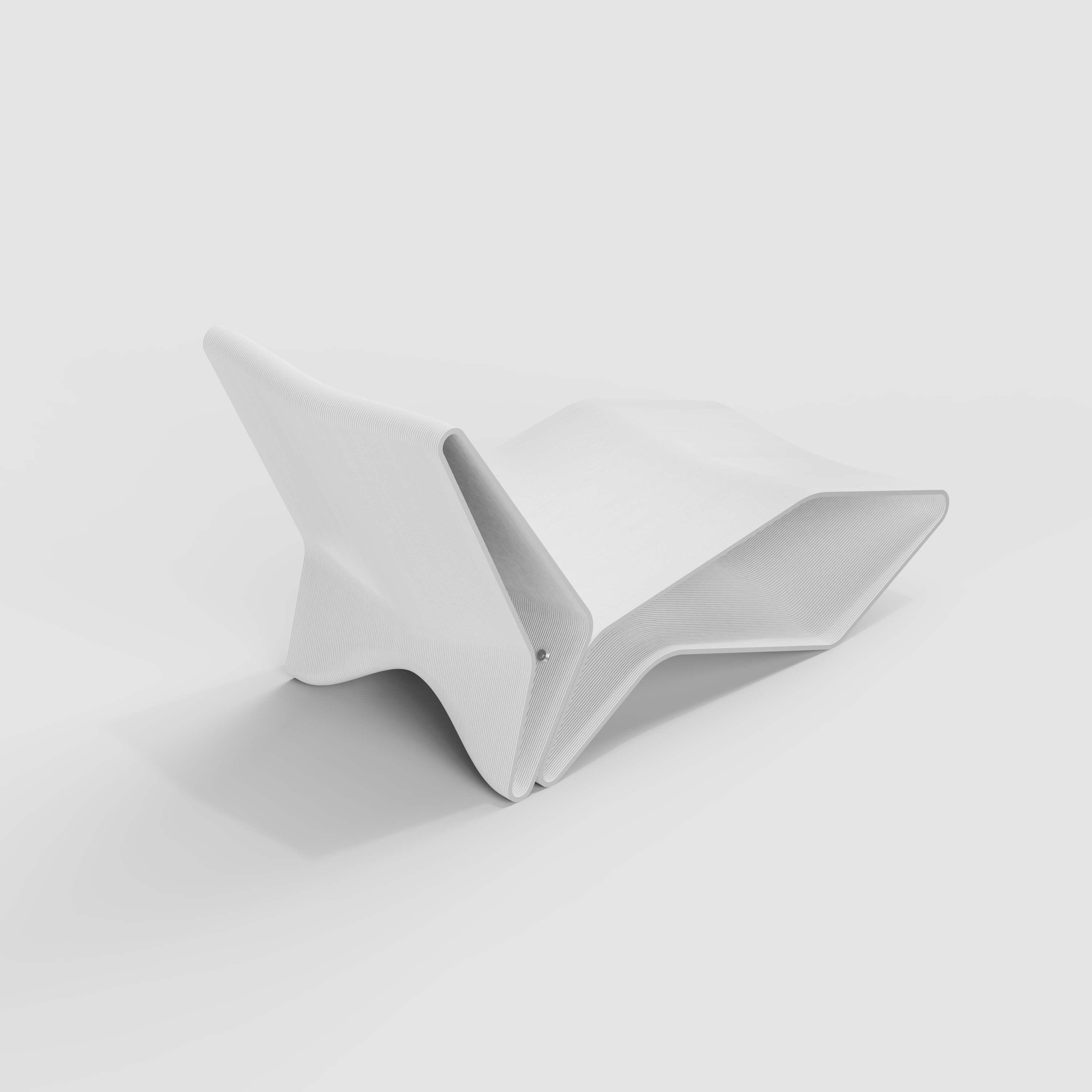
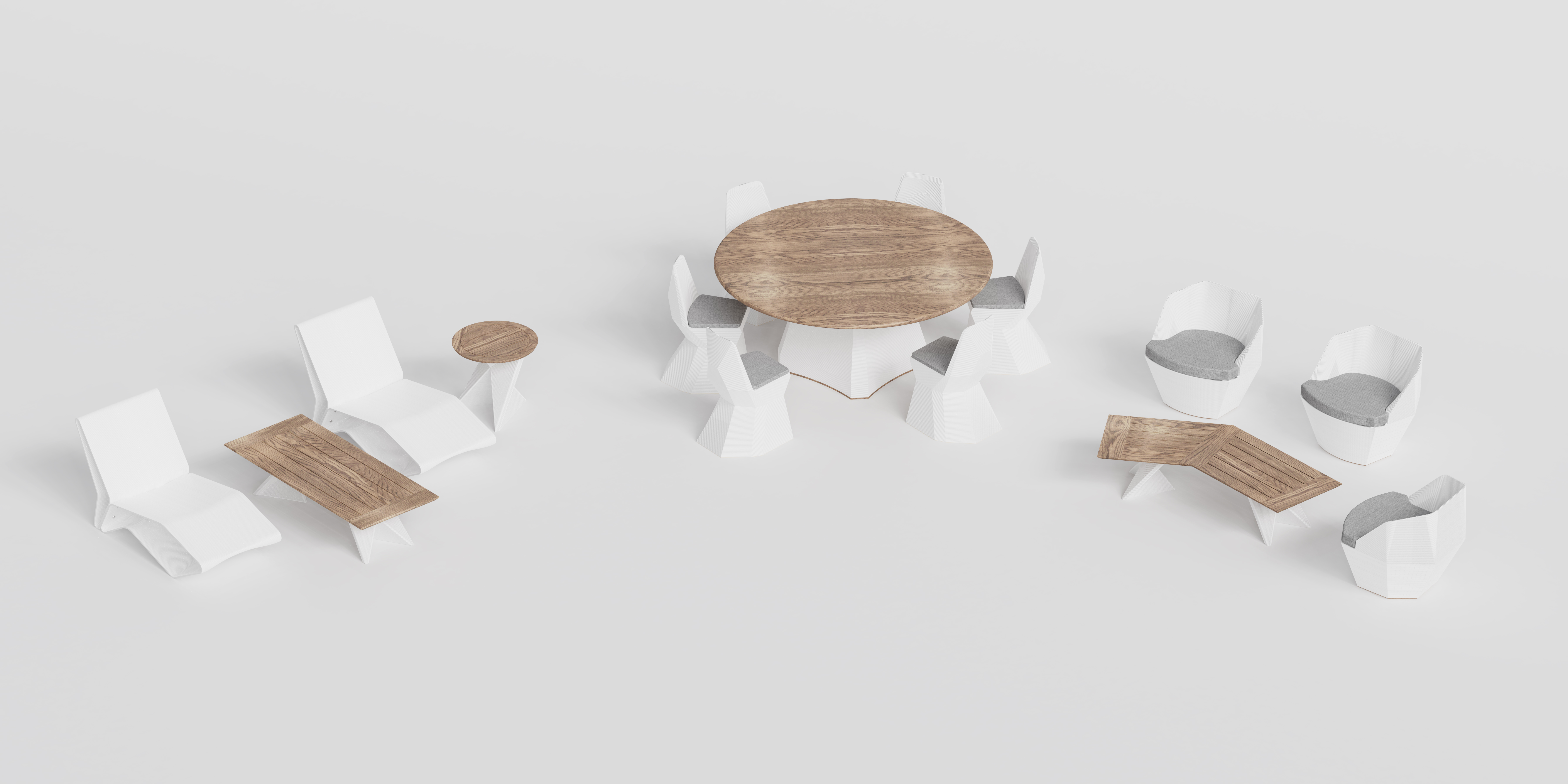
Manufacturing Process: Kyanite Chair
The Kyanite Chair was a challenge to develop. I had a professor tell me once, "you have to design about 50 chairs to design 1 chair." His point was, a chair is not only difficult to nail ergonomically on the first go, but it also one of the most used and abused pieces of furniture and needs to be just as durable as it is comfortable.
This is where additive manufacturing shines. Not only can I use desktop 3D printers to quickly prototype new concepts, but our large scale printers are just as fast. Because the layer height and wall thickness gets scaled along with bed size, the print time on these large pieces is only about 6 hours. This allowed me to make changes in CAD and and have a full scale 3D model the next day. This was invaluable in figuring out the ergonomics, structural integrity and manufacturing order of operations for this piece.
Below you can see the internal structure and two part print connection that makes this chair construction possible.
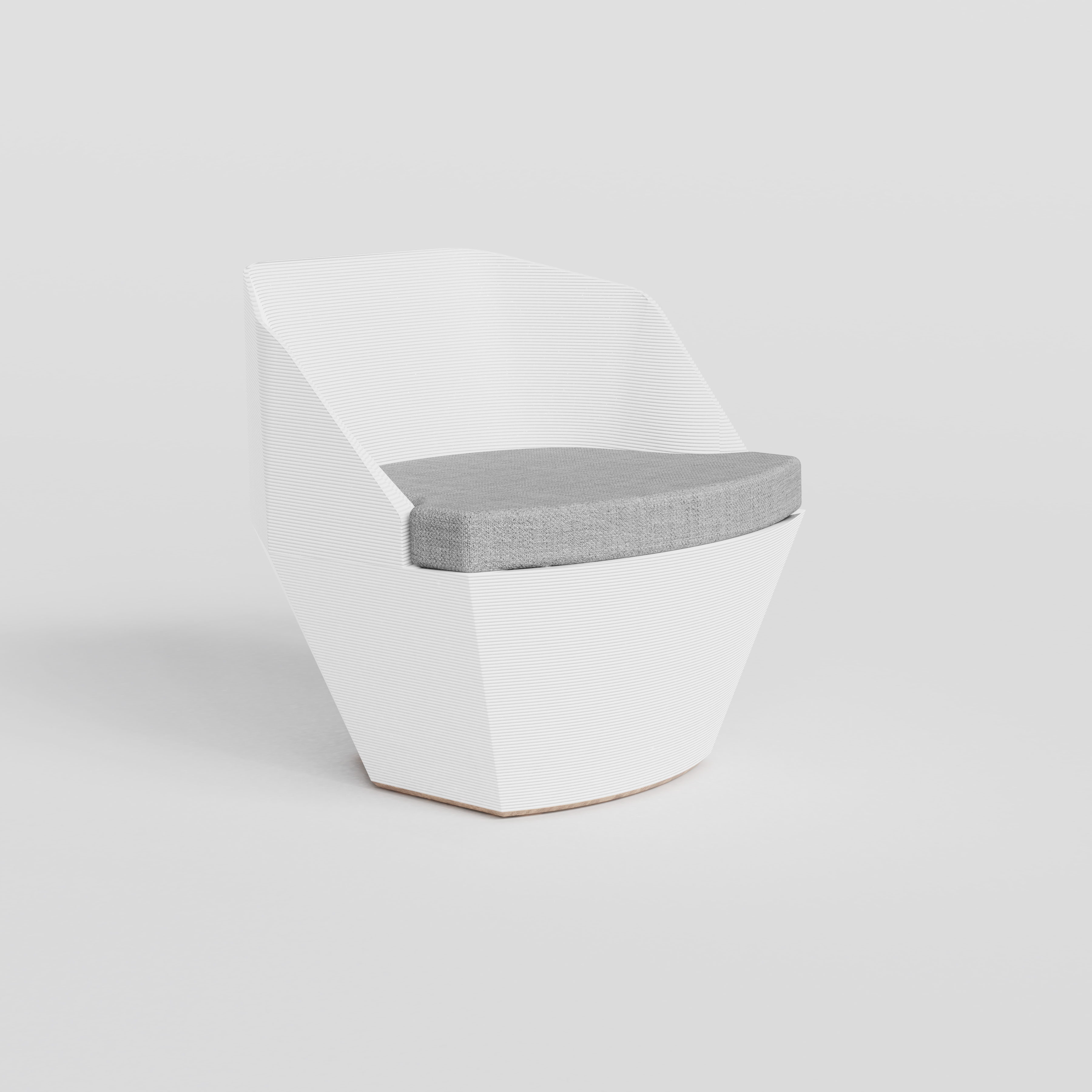
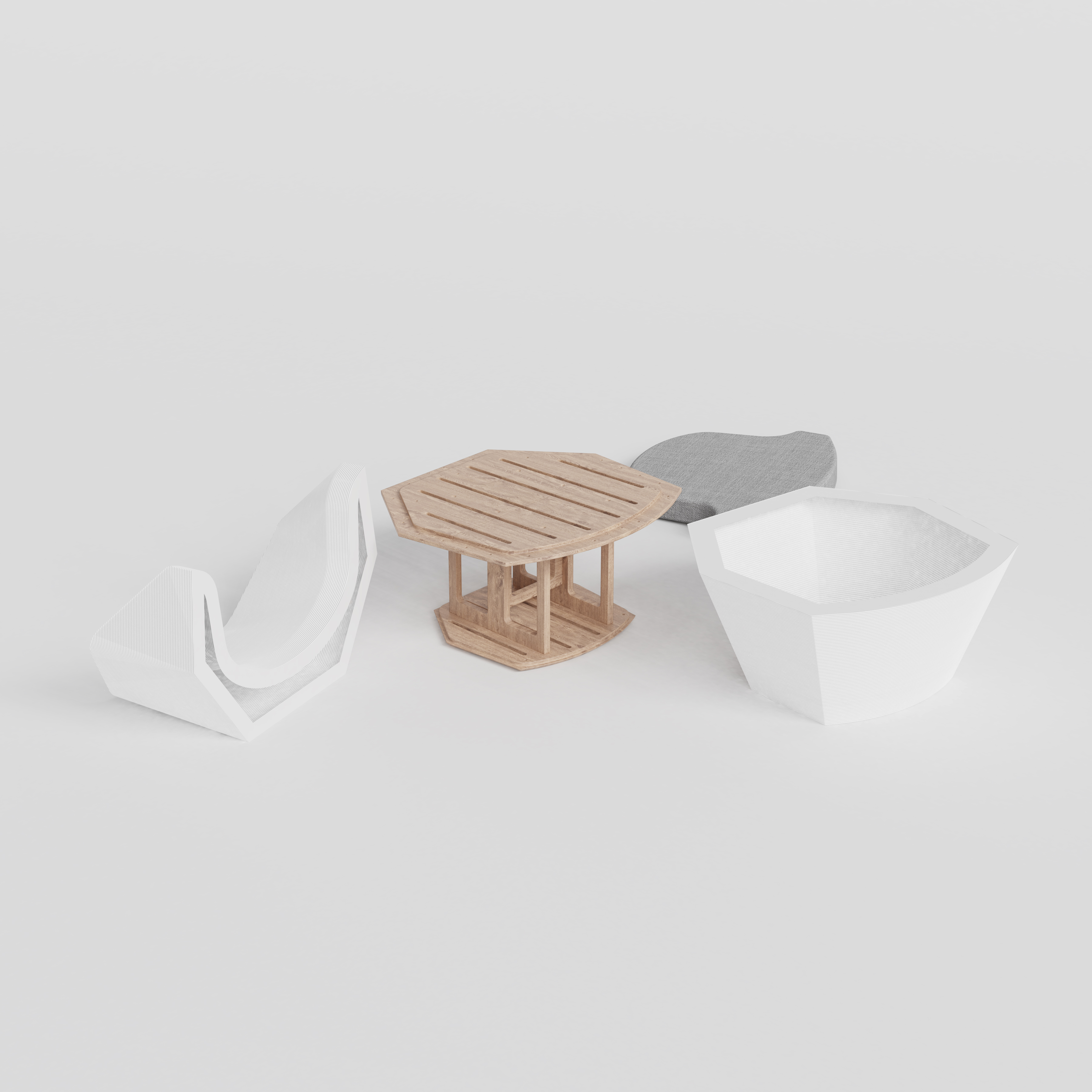